Central Utility Plants (CUPs) don’t often take the spotlight on massive campus-wide construction projects. They can seem sterile and uniform in their functionality and their constructability. But for those of us who live and breathe CUPs we know and appreciate their essential role in delivering smooth operations for buildings and the people who occupy them.
There are times when planning for a CUP can bring monumental challenges and have the potential to define the direction of an entire project. This is what we experienced in Austin on the Texas Facilities Commission (TFC) Capitol Complex project.
JE Dunn managed the excavation, utilities, and CUP work for phase one of the TFC Capitol Complex project. The CUP was construction of a new central utility plant, known as 3CUP, and a half-mile utility tunnel that would serve the new office buildings and existing ones.
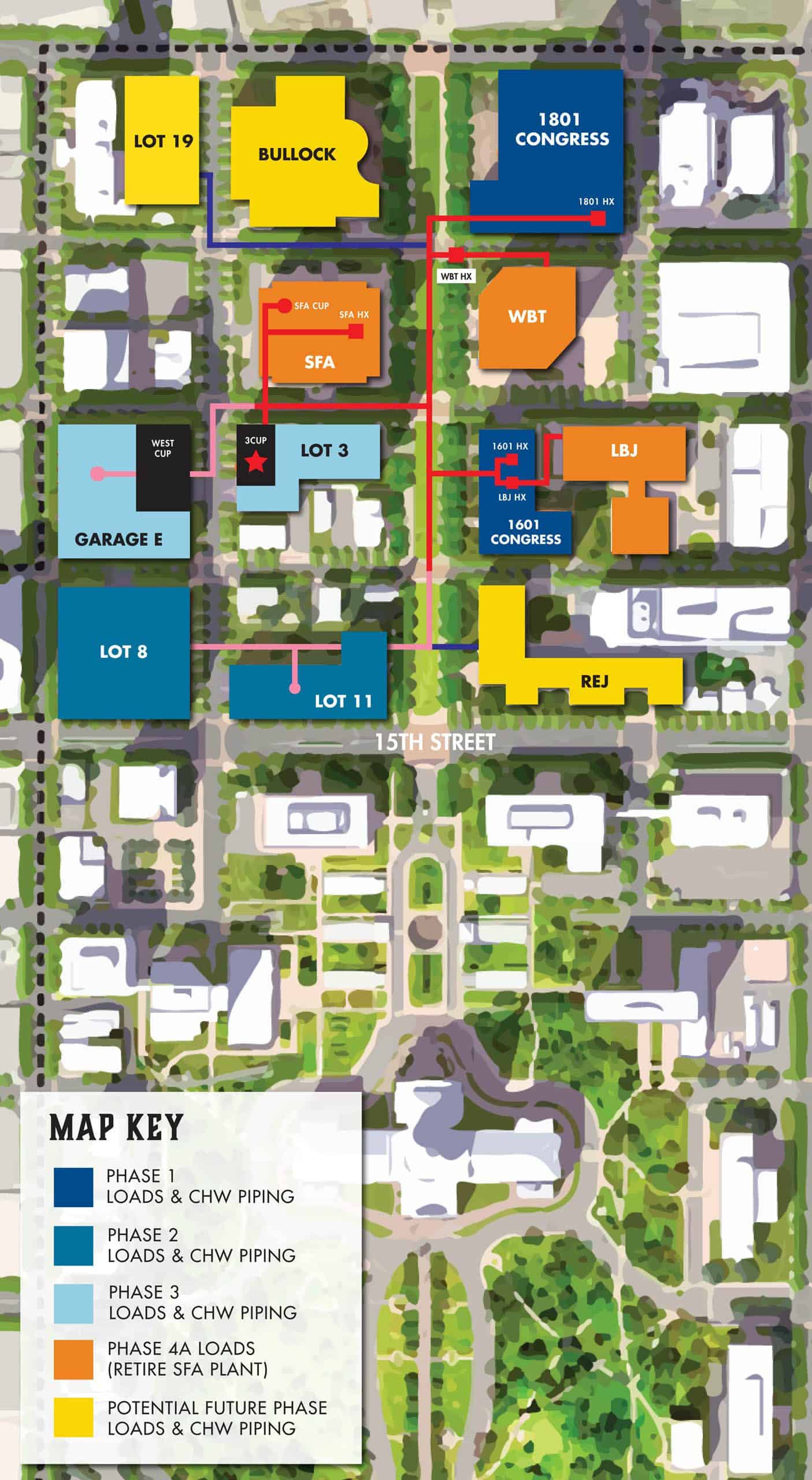
Everything south of 15th Street as shown in the map was originally fed by the Stephan F Austin plant. 3CUP would expand current and future services to this southern campus which was the location for phase 1 construction for the Capitol Complex.
The challenge we faced began with location and operation of the existing central utility plants.
The power and utility services that fed the existing downtown offices and adjacent buildings were divided by 15th Street. Everything south of 15th Street was fed by the Sam Houston plant and everything north was fed by the Stephan F. Austin (SFA) plant.
Originally, 3CUP was going to be located by the southern Sam Houston plant but feed the new and existing office buildings on the northern side. However, building the tunnel was going to be costly, and after further review, the client and design team determined there was not enough electrical system infrastructure to make this an option.
TFC needed a new solution, and together, JE Dunn and Jacobs engineering firm proposed a solution: Build the CUP on the new site and use the existing SFA utility tunnel to connect the new plant to the SFA plant.
This scenario guaranteed that there was enough redundancy for the north campus and allowed 3CUP and SFA to be one operating system rather than two separate plants. And once the project team began looking at 3CUP and SFA as one system, they realized it was over designed for redundancy, taking 3CUP from a +2.5 redundancy to an N+1.
TFC approved the option, and our collaborative problem solving led to:
- Improved schedule by eliminating four temporary shutdowns that were originally planned with the first design and location of the CUP.
- Better location adjacent to Congress Street, near the new green mall, which minimized the piping distribution length.
- Improved constructability for future expansion of 3CUP. The site provided enough space to fulfill the long-term chiller plant needs for the new master plan while reducing the existing utility relocation requirements significantly. It also supported enhancements to the SFA plant.
- The ability for TFC to take advantage of the Austin Energy SFA Vault which enabled 3CUP to be dual fed vs single fed which added another layer of electrical redundancy not afforded at the Sam Houston Site
- $2.5 million in savings to TFC.
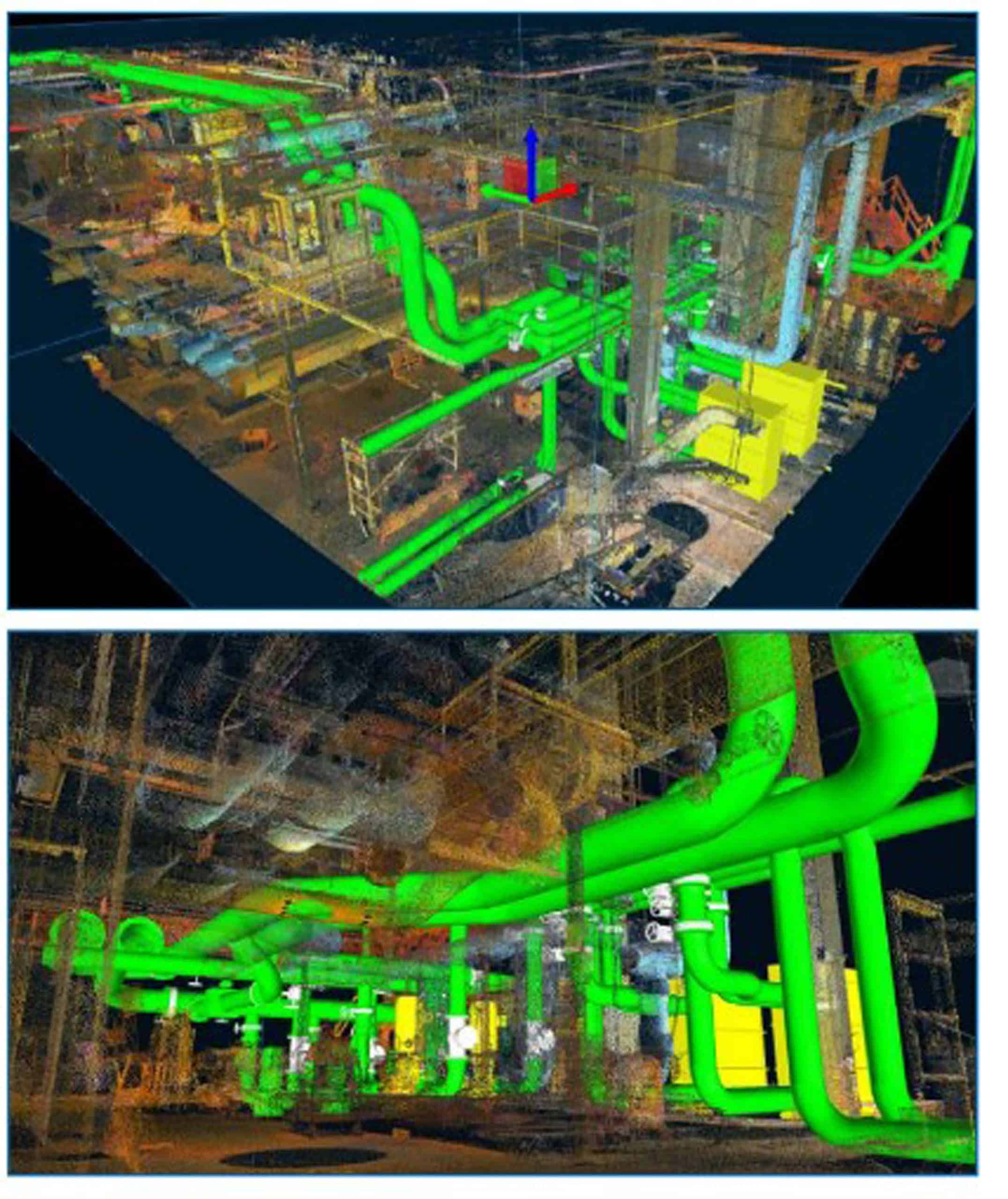
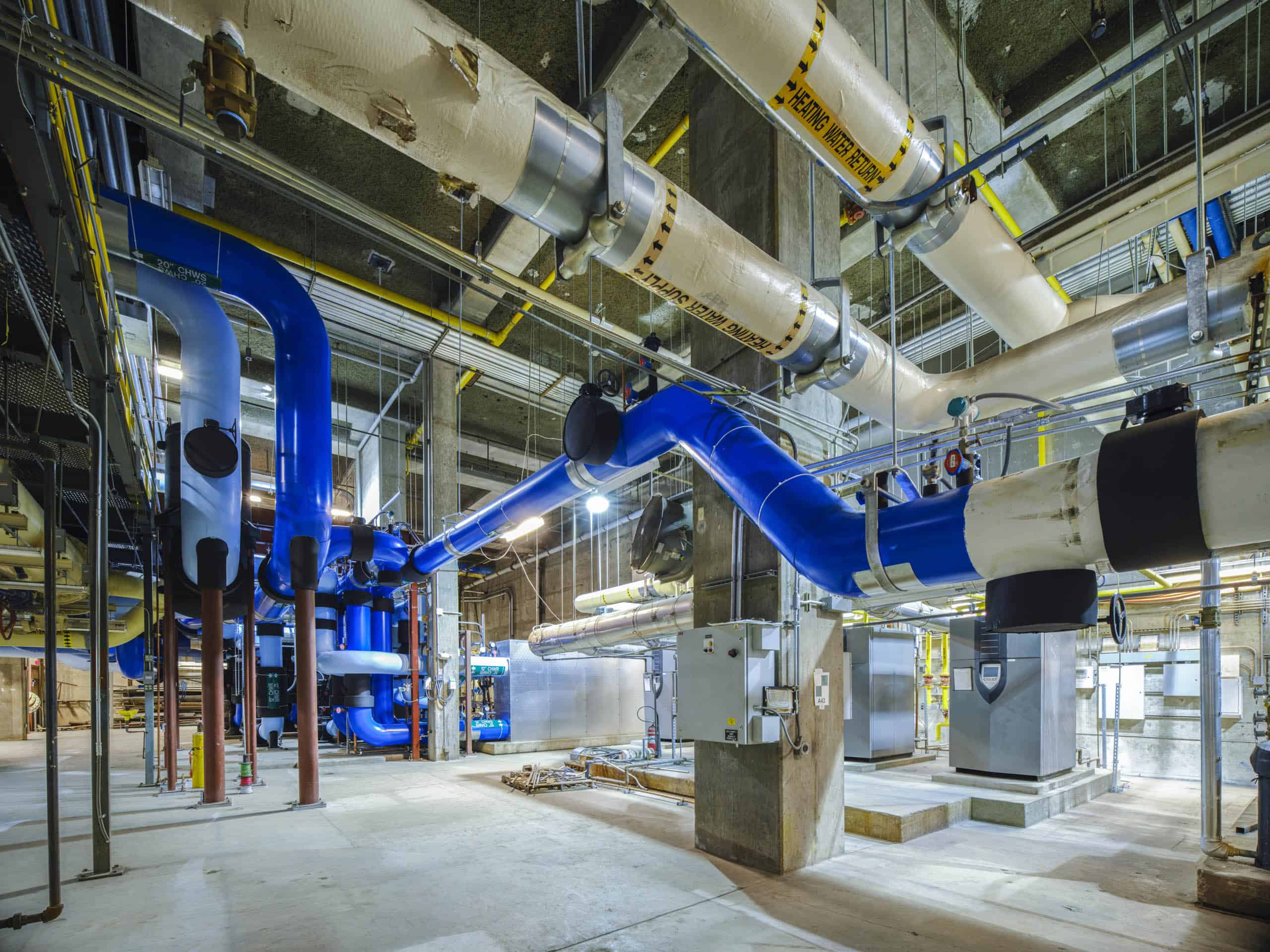
Renovations and additions to the existing SFA central utility plant proved to be more challenging than constructing a new plant due to the space constraints. In some places, new piping was installed inches from existing piping. Virtual Design and Construction (VDC) was critical to ensuring smooth and accurate installation. To tie the new and existing plants together without a shutdown to service to existing buildings, the project team used a pipe freezing method that allowed frozen water to temporarily be used while the connection was made.
“JE Dunn brought true engineering services through the arm of a general contractor. We functioned as an in-house peer reviewer providing engineering calculations, verification of scope and materials, and constructability reviews,” said Dave Barber, National Engineering Services Director at JE Dunn, “and part of our proposed solution was to also bring trust, comfort and insurance that the systems in place would work properly upon final completion and through the life of the system.”
The relationship and trust built between Dynamic Systems, Inc. (DSI), JE Dunn, TFC and Jacobs resulted in JE Dunn and DSI providing additional commissioning, test and balance assistance, and general oversight for completion of Phase 1 of the Capitol Complex project. That also required JE Dunn to coordinate with two other general contractors to ensure their projects tied correctly into the 3CUP system.
For the last decade, Barber has worked to build JE Dunn’s MEP department, which includes more than 100 ME experts throughout the U.S. As more projects are delivered through design assist or design-build methods, having the general contractor provide true ME services becomes a significant advantage for the client.
“I think JE Dunn undersold its real capabilities for this kind of ME work. The team’s ability to consistently maintain personnel to work on the ME issues was a great benefit to the overall success.” said Keith Hall, retired TFC Senior Facilities, Design & Construction Project Manager. “JE Dunn took care of all aspects of the project without a question of their capabilities.”
For example, JE Dunn was part of the new design scheme to de-couple the main chilled water system from the building systems with plate and frame heat exchangers, resulting in a simpler and easier-to-control system. This scheme increases reliability and maintainability, by allowing TFC to isolate the systems without having to drain sizable portions of piping.
JE Dunn’s ME team also helped the project save capital dollars by increasing the delta T from a traditional design of 10 degrees to 14 degrees. This change would put 40% more capacity into the same size distribution pipe. In this case, however, we were able to install smaller piping and achieve the designed capacity needed for the overall system, which saved money for TFC.
The functionality of central utility plants is constantly changing to adapt to technology, environmental regulations, and sustainability. Carbon neutral plants, high-efficiency boilers, and heat recovery systems are part of the conversations to minimize CUP environmental impact. Even now, the industry is getting ready to switch refrigerants again, as the Global Warming Potential (GWP) of refrigerants becomes a more important focus of how buildings contribute to global warming. A GWP of zero is the goal.
Those considerations will matter as more healthcare campuses, universities, city districts, airports and other large institutions expand, upgrade, and build new CUP facilities that are more sustainable.
And yes, our ME specialists have a technical understanding of how central utility plants operate and the changing technology. But more importantly, they have relevant experience to properly apply this technology to a client’s project that makes sense for their project scope and business goals.
This is the value that JE Dunn brought to TFC.
And what I’ve encountered in my five years working with JE Dunn is that our skill in engineering application allows us to have deeper relationships with engineering firms that result in this level of problem solving, design reconfiguration, and cost reduction the project team delivered to TFC.
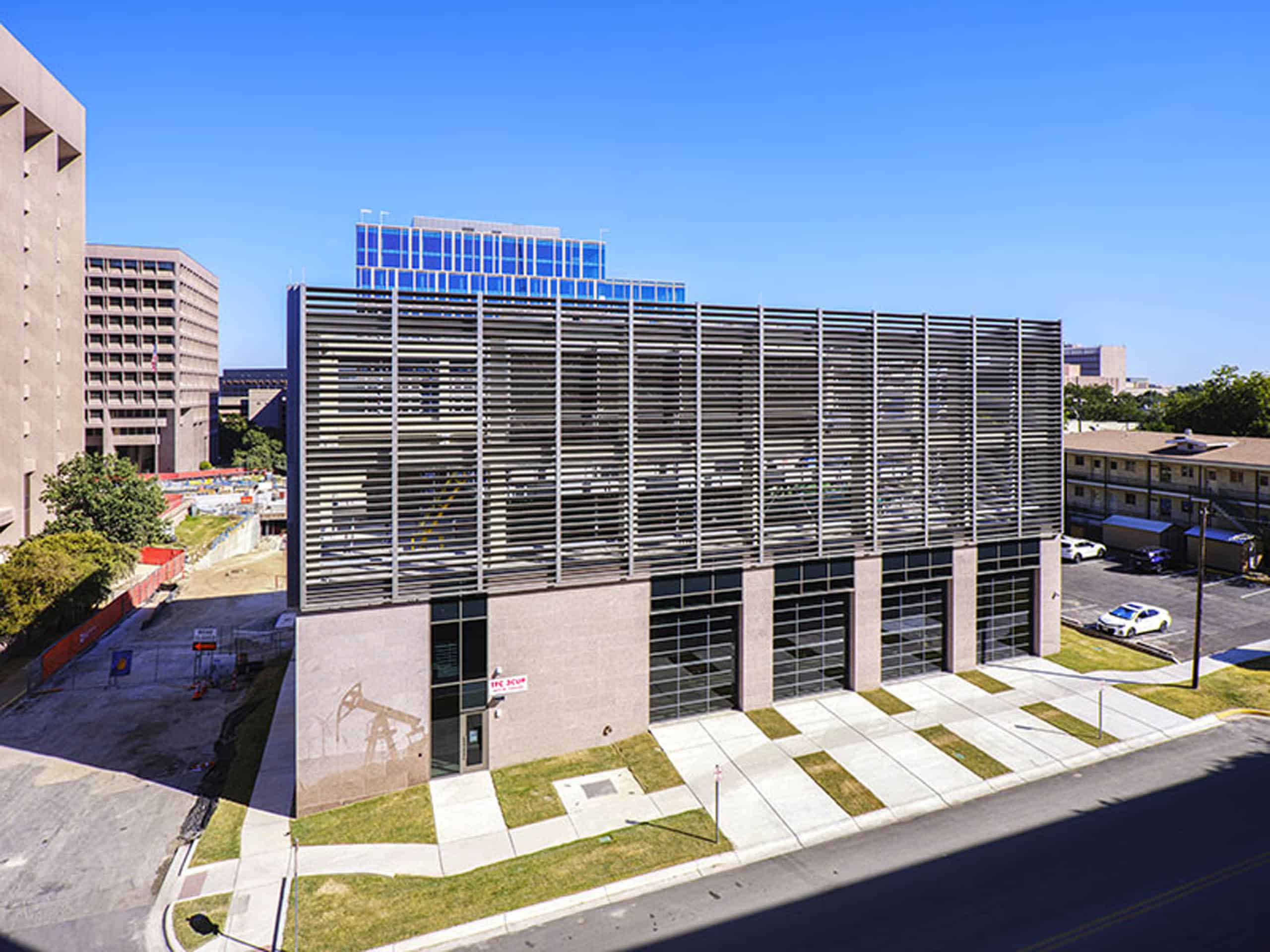