At JE Dunn Construction, addressing these challenges goes beyond operational efficiency; it’s about creating a culture where every individual thrives. The “Flow Like Lasso” initiative adopted by our Blue Springs School District (BSSD) project team and client, inspired by the leadership lessons from the popular television series Ted Lasso, exemplifies this approach.
The challenge: building cohesion in adversity.
The BSSD project faced unique hurdles, including:
- A Construction Manager Agency (CMa) approach with public bid trade partners who weren’t familiar with each other.
- A tight project schedule exacerbated by COVID-related labor and supply chain issues.
- A young and unfamiliar team.
- Contention with city leadership and community members neighboring the construction site.
The stakes were high, and overcoming these challenges required a cultural shift that prioritized positivity, collaboration, and resilience.
The solution: “flow like lasso” in action.
As the job got underway, project Superintendent, Eric Neill, encouraged everyone to watch the television series, Ted Lasso. Soon, most of the team was watching the show. It wasn’t long before Project Manager, Darren Younker, Lean Manager, Dan Shipley, Eric and I saw the opportunity to address the challenges noted above in a new way, implementing seven Lean leadership principles with a Ted Lasso twist.
1. Believe – be optimistic and believe in people. 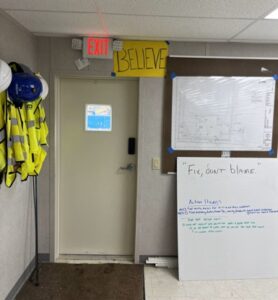
On the BSSD project, the CMa method created a complex environment with multiple parties contractually bound to different aspects of the work. This dynamic can cause teams to become siloed, losing a sense of camaraderie that is essential for success. To foster a ‘believe in the best of people’ mentality, the team organized monthly Bond Project Meetings. These gatherings united bond participants, including two competing construction managers, the architect and the school district as one unified team. By focusing on collaboration and a shared goal, the project team built trust and optimism across all stakeholders.
2. Utilize the locker room – build trust and make the “locker room” a safe space.
Creating a safe and trusting team environment starts with open communication. The BSSD project team embraced this by tackling tough conversations and challenging each other to improve. A standout example was during Skin Coordination meetings, where JE Dunn’s Quality Assurance team, trade partners, and the architect collaborated to meticulously review the building’s exterior skin. While the architect admitted it was difficult to have their work scrutinized, the process led to a better product delivered more efficiently. This commitment to honest dialogue exemplified the power of the ‘locker room’ mindset—facing challenges together to achieve success.
3. Be the best version of yourself – fix, don’t blame. When things go wrong, it is often the system, not the person.
The CMa method used for the BSSD project brought together trade partners through public bidding, meaning many team members were unfamiliar with each other. With no time to build a team rapport before the project, the group embraced a ‘fix, don’t blame’ mindset. By addressing challenges at the systemic level rather than pointing fingers, they cultivated a culture of collaboration and problem-solving—showing what it means to strive for the best version of themselves, even in a fast-paced, high-stakes environment.
4. Be a goldfish – they are the happiest animal on the planet with a 10 second memory. When things go wrong, learn and move forward. Don’t get stuck! 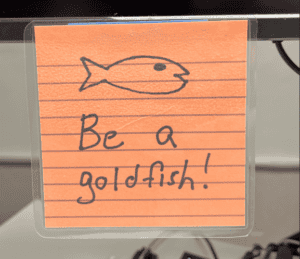
When things go wrong on a construction site, it’s easy to dwell on the obstacles. But the project team embraced the ‘be a goldfish’ mentality—learning, letting go and moving forward. After a particularly tough day, I left a sticky note with a hand-drawn goldfish on a colleague’s desk as a lighthearted reminder to stay positive. Small gestures like this helped the team support each other and maintain a high-energy, forward-focused culture, even on the hardest days.
5. Celebrate your wins – it doesn’t matter how small the celebration is; we just need to recognize people’s efforts. It motivates them!
The CMa method and a tight budget left little room for team-building activities. However, the project team found creative ways to celebrate their wins and boost morale. They organized a monthly team lunch, held safety raffles with prizes like prime parking spots and swag, and surprised the crew with popsicles on hot days. These small yet impactful gestures kept the team motivated and strengthened their bond, proving that celebrating success doesn’t have to come with a large price tag.
6. Round up the diamond dogs – get out of work mode and connect as people. Keep it informal – when things get “scheduled and big” it’s often not as personal.
This was as simple as sending out a last-minute text at the end of the day to ‘round up the diamond dogs’ for an after-work hang at a local pub.
7. Be curious, not judgmental.
The team embraced the idea that everyone has something valuable to contribute and that curiosity builds stronger teams. Instead of top-down decisions, they sought input from those closest to the work—engaging directly with workers and even high school students in the community. A standout example was the design of a roundabout at the main entrance of an active school district. By inviting high school students to share their ideas, the team discovered practical solutions that worked for everyone. This approach highlighted the power of curiosity over judgment, fostering collaboration and innovation.
“Our industry has a hallowed tradition of telling each other who, what and how we’re screwing up. We’re trained to focus on the negative and spend an inordinate amount of time and talent trying to prove it to each other. That way of work is unnatural to me and has been a struggle for 40 years. My Lean journey has given me tools to change this peculiar institution. Watching Ted Lasso lead by earning trust and helping people make good decisions was fun and heartwarming. Ted’s talent for play, vulnerability, recognizing everyone, being present, using rituals to build trust and most important to me, guiding the team to know how they are greater than the sum of its parts felt like a Lean parable. Barbeque Sauce.” – Superintendent, Eric Neill
The results: a culture of excellence
The outcomes of the initiative were transformative:
- A sense of family and camaraderie emerged among the team, extending beyond professional boundaries.
- The project met its schedule amid COVID challenges and used less than 1% of the owner’s contingency fund.
- The owner, designers and trade partners became advocates of each other, eager to collaborate on future projects.
- Community members neighboring the jobsite who once disliked the construction became fans of the team by the end of the project! The project team also salvaged some of the windows from the building demo and gave them back to the neighbors to use rather than sending them to the dump.
Key takeaways for jobsite culture
- Positive, people-centered leadership drives measurable results.
- Establishing a collaborative culture early can turn new, untested teams into high-performing groups.
- A focus on empowerment, empathy, and resilience creates advocates out of clients and team members alike.
Conclusion: Flowing into the future
When Eric introduced our team to the show, seeing Ted’s leadership approach and how closely it tied to Lean principles was a game-changer on how we approached our project. Through a very challenging time in the construction industry, we were able to create a culture where people were excited to work, felt heard and were empowered to share their opinions and ideas. Chris Koch of Hollis + Miller Architects as well as Dr. Charlie Belt and Seth Shippy of the Blue Springs School District were instrumental in helping us implement this culture.
It is so vitally important to stay curious on your project. Every day onsite, there are professionals working who have years of knowledge, experience and creative genius to improve the site. Take the time to stop and listen, and you’ll be amazed at how much better they make your project.
By adopting this initiative, JE Dunn continues to lead the industry in cultivating jobsite cultures that inspire excellence, innovation, and repeat partnerships. The ‘Flow Like Lasso’ initiative at Blue Springs School District demonstrates that a construction project is as much about building relationships as it is about building structures.